In the competitive world of manufacturing, maintaining high-quality standards is paramount. One of the most effective strategies to ensure consistency and excellence in production processes is the implementation of Layered Process Audits (LPAs). These audits, designed to ensure process compliance and promote continuous improvement, are fast becoming an integral component of quality management systems.
Understanding Layered Process Audits
Layered Process Audits are systematic, planned evaluations conducted across multiple layers of an organization. They are designed to validate adherence to Standard Operating Procedures (SOPs), ensuring the production process is performed correctly and consistently, thereby enhancing the quality, safety, and efficiency of products or services. LPAs involve personnel from various management tiers, each with a distinct focus and scope of assessment.
The Essence of LPAs
The primary objective of LPAs is to shift the focus from inspecting the finished product to monitoring and validating the processes that produce them. This proactive approach emphasizes the importance of consistently following operational procedures, maintaining quality standards, rectifying deviations at the earliest possible stage, and driving continuous improvement.
The Layers in LPAs
The 'layers' in Layered Process Audits refer to the multiple levels within an organization that participate in the auditing process. These layers typically include:
- Frontline Employees and Operators: These individuals conduct audits within their workstations or areas, focusing on adherence to safety standards and SOPs.
- Team Leaders and Supervisors: These personnel play a pivotal role in conducting audits, primarily verifying that team members follow established procedures and safety protocols.
- Managers and Directors: Middle managers participate in LPAs to assess overall performance, reviewing processes, resource allocation, and efficiency.
- C-Level Executives: Senior management engages in LPAs to gain a high-level view of the organization’s processes, focusing on strategic aspects such as alignment with organizational goals and regulatory compliance.
- Cross-functional Teams: These teams collaborate to address non-compliance identified during audits, ensuring comprehensive strategy for overseeing quality, safety, and efficiency control.
- Quality Assurance and Continuous Improvement Teams: These teams coordinate the audit schedule, provide training, and promptly take corrective actions, playing a crucial role in fostering a culture of accountability.
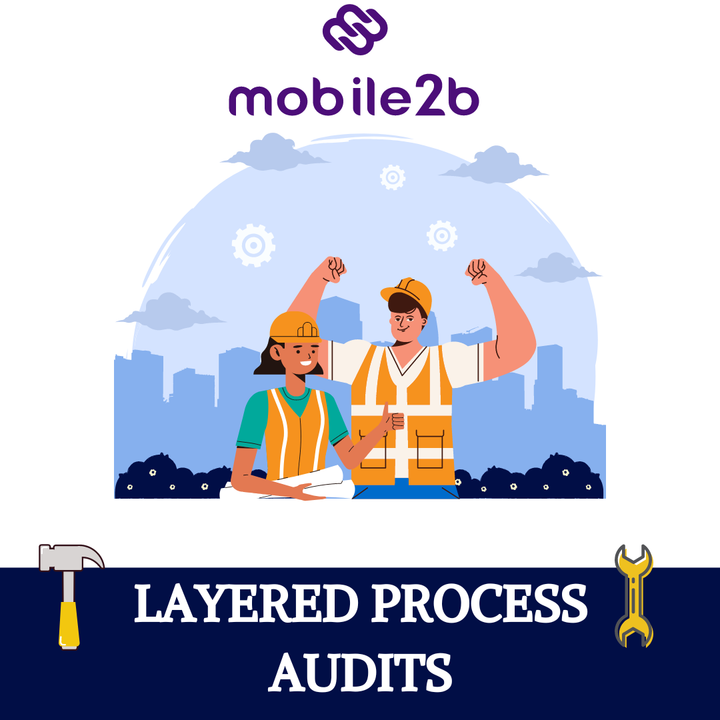
The Importance of LPAs
- LPAs are indispensable for process improvement, quality, and safety control. They offer several benefits:
- Limiting and Controlling Risks: LPAs identify and mitigate process-related risks, reducing the probability of errors, inconsistencies, and deviation.
- Improving Quality: Regular verification of standards and procedures enhances operations, reduces customer complaints, product recalls, or rework.
- Ensuring Compliance: LPAs demonstrate compliance with various certifications and guidelines, including ISO 9001, IATF 16949 (for automotive quality management), ISO 45001 (for safety management), and ISO 14001 (for environmental management).
- Fostering a Culture of Excellence: Implementing LPAs fosters a culture of continuous improvement within the organization, encouraging employees at all levels to identify process enhancements and opportunities for improvement.
- Digitizing LPAs: The Way Forward
The transition from traditional paper-based audits to digital Layered Process Audits offers numerous advantages:
- Faster and More Efficient Audits: Digital LPAs make the audit process quicker and more efficient. User-friendly interfaces allow auditors to complete audits in less time than required for paper-based audits.
- Improved Management of Corrective and Preventive Actions (CAPAs): Digital LPAs facilitate prompt identification and resolution of issues, reducing the time lag between issue identification and resolution.
- Standardized Document Version Control: Digital LPAs ensure up-to-date audit forms and checklists are available across the organization, simplifying comparisons across different sites and versions.
- Instantaneous Metrics and Data Analysis: Digital LPAs enable real-time data collection, ensuring that audit results are readily available, allowing swift corrective actions.
- Enhanced Data Security: Technology-based audits are encrypted to protect data from unauthorized access, providing higher data security than paper-based audits.
- Reduction of Hidden Costs: While paper-based systems may seem cost-effective, they often entail hidden costs in terms of time and effort spent on paperwork. Digital LPAs eliminate these hidden costs.
A tool like Mobile2b, with its user-friendly Drag-and-Drop platform, can be a game-changer for organizations looking to digitize their LPAs. This robust solution makes it easy to integrate, automate, and streamline the LPA process, resulting in improved efficiency, accuracy, and productivity. The Layered Process Audits offer a comprehensive approach to quality management, enabling organizations to improve safety, reduce costs, enhance customer satisfaction, drive continuous improvement, ensure compliance, and cultivate a culture of quality throughout the organization. Start your Digital Layered Process Audits journey now - Try our LPA App for free or book a demo.
Implementing Layered Process Audits
The implementation of an LPA program requires a systematic approach. Here are the critical steps to consider:
- Learn About LPA Best Practices: Understand the concept, benefits, and best practices of LPAs. Resources like the Automotive Industry Action Group’s CQI-8 Layered Process Audits Guideline can provide valuable insights.
- Assemble a Team: Form a cross-functional team with representatives from various management levels and departments. Define clear roles and responsibilities for each team member.
- Identify Processes (LPA Scope): Outline the processes that require auditing. These could include safety protocols, quality control procedures, and more.
- Create Audit Checklists: Develop detailed checklists to comprehensively cover each step of the audited processes. These checklists serve as a guide for auditors to evaluate compliance.
- Assign Auditors: Assign individuals from each management level to conduct audits.
- Schedule Auditing Frequency: Set regular audit frequencies in auditors’ calendars to increase ownership and adherence to best practices.
- Conduct Audits: Regularly conduct audits using checklists. Auditors verify the processes and identify any non-compliance.
- Document Findings: Document audit findings, including positive observations and areas requiring improvement. Delegate these to the appropriate team for action.
- Analyze Data: Analyze audit data to identify trends, recurring issues, and potential areas for process enhancement.
- Manage Corrective and Preventive Actions: When discrepancies or issues are identified, define actions, escalate or assign them to the right management layers.
- Feedback Loop: Share audit results and improvement actions with relevant stakeholders. Transparency is critical to building awareness and accountability.
The Impact of LPAs on Quality Control
Layered Process Audits can significantly transform the quality control landscape in manufacturing. By focusing on process compliance and standardization, LPAs can help companies reduce defects, ensure consistency in production, and improve overall product quality.
While LPAs require an initial investment in terms of time and resources, the long-term benefits far outweigh the costs. The reduction in errors, inconsistencies, and deviation leads to improved quality performance metrics, ultimately boosting customer satisfaction and the company's bottom line.
Furthermore, the implementation of LPAs fosters a culture of continuous improvement. It encourages employee engagement through active participation in the auditing process, which in turn leads to a more unified and quality-conscious workforce.
In conclusion, Layered Process Audits are an essential tool for any manufacturer seeking operational excellence. By promoting process verification, fostering a culture of continuous improvement, and leveraging digital solutions like Mobile2b, companies can significantly enhance their quality control practices and achieve superior performance. So, start your digital transformation journey today and leverage the power of LPAs to drive quality enhancement and operational excellence in your manufacturing processes.